PARAMETERS FOR SPDs SELECTION
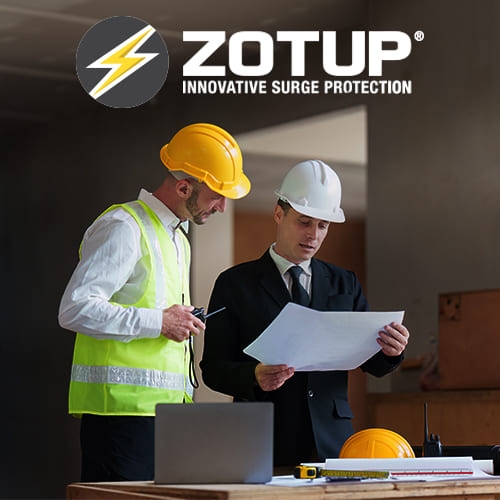
ZOTUP SPDs WITH PROGRESSIVE PERFORMANCE INDICATOR
SPD efficiency state is now simplified. A progressive indicator from green, to orange and then red, allows you to check in a simple and immediate way the level of protection that the SPD is still able to offer to the system. The assurance of being able to control progressively the level of efficiency of the SPD and then to program its replacement, is our first point of strength. More than these features, ZOTUP surge arresters present many components: integrated fuse function in case of failure of the SPD and the possibility to use the SPD in environments with a high pollution rate (grade 3).
VIDEO - ZOTUP INTRODUCTION
Discharge capability is an important parameter when choosing a suitable SPD, but there are also other parameters to be considered.
The main ones are:
- Suitability for the power distribution system (TN, TT, IT);
- Maximum Continuous Operating Voltage (Uc);
- Behaviour in case of TOV (UT);
- SPD Type (impulse current/voltage) T1, T2, T3;
- Short circuit withstand capability/short circuit current rating (Isccr);
- Back-up protection OCPD (fuse);
- Follow current interrupt rating (Ifi);
- Voltage protection level (Up);
- Pollution Degree;
- Response time (ta).
- Maximum Continuous Operating Voltage Uc:
This is the maximum r.m.s. voltage, which may be continuously applied to the SPD's mode of protection.
It is selected depending on:
- the nominal voltage of the circuit to be protected;
- the low voltage distribution system (TN, TT, IT);
- the required modes of protection (phase to earth; phase to neutral; neutral to earth).
Immunity against commonly specified TOVs (Temporary Overvoltages) for 230/400 V low voltage systems is guaranteed by selection of the following Uc values:
Short circuit withstand capability (short circuit current rating Isccr):
During the normal operation of overvoltage protectiove devices, the SPD provides a high impedance at nominal system voltage and rated frequency. In case an SPD reaches its end-of-life in a low impedance state, the resulting short-circuit current must be interrupted. This interruption may be provided by an SPD internal disconnector or in conjunction with an external disconnector, e.g. a fuse.
When the SPD manufacturer provides information about a maximum allowed backup fuse rating, any alternative overcurrent protective device, like e.g. MCBs or circuit breakers, must be considered very carefully, because such devices may not provide the required impulse withstand, specifically in applications where type 1 SPDs are required and partial lightning currents are to be expected.
If other kinds overcurrent protective devices than the ones recommended by the SPD manufacturer are used, this is under the full responsibility of the installer. Furthermore the higher internal impedance of such other devices compared to a fuse may add to the voltage drop under surge conditions and may therefore worsen the effective voltage protection level for the installation and equipment.
Follow current interrupt rating Ifi:
This rating only exists in the IEC 61643-11 and relates to SPD constructions, which generally cause a follow current from the power supply after discharge current flow, and describes the ability of such SPDs to self-extinguish such follow current without operation or alteration of any disconnector. Important for correct understanding is, that this parameter does not provide a real current value that gets interrupted by the SPD, but the maximum prospective short circuit current that may be available at the SPD's point of installation, at which any expected follow current will be self-extinguished by the SPD.
While IEC 61643-11 allows this follow current interrupt rating Ifi to be lower than the short-circuit current rating Isccr, EN 61643-11 requires this rating to be equal to the short-circuit current rating Isccr. But both installation rules, IEC 60364-5-534 as well as HD 60364-5-534, require that the follow current interrupt rating must be equal or higher than the maximum available short circuit current from the power system at the SPD's point of installation.
NFC No Follow Current®:
Thanks to their design characteristics, SPDs with No Follow Current® technology (NFC), completely avoid the flow of follow currents from the power system at all, and therefore also limit the impulse stress to disconnectors (e.g. fuses) and upstream protective devices in the installation to a minimum. Thus resulting in a lower risk of supply outages.
Voltage Protection level Up:
This parameter is defined as the maximum instantaneous voltage value at the SPD's terminals during its intended operation under defined impulse stress conditions. Depending on the construction and the type of components used in the SPD this protection level corresponds to:
- for voltage Limiting SPDs: the residual voltage at nominal discharge current (8/20 µs) for type 2 SPDs or the residual voltage at a discharge current (8/20 µs), with a crest value of Iimp for type 1 SPDs;
- for voltage switching and Combination SPDs: the limiting voltage at 1,2/50 μs voltage impulses and the residual voltage as above, whatever is higher, or the limiting voltage at hybrid generator impulses.
The protection level provided by SPDs must be compared to the impulse voltage withstand of the equipment to be protected, also taking into consideration the distances between these SPDs and the equipment.
Response time ta:
In EN 61643-11 the response time of SPDs is not directly addressed, but only an implicit factor when testing for the limiting voltage of voltage switching or combination SPDs. However, for semiconductors even very short peaks can be harmfull and therefore the response time of SPDs is not of secondary importance.
The phenomena of transient overvoltages in equipment is usually in the order of some ten μs, the response time of voltage limiting SPDs is in the order of some to some ten ns, but the time before damage may occur to some categories of semiconductors is in the order of ps.
This leads to the simple statement: the shorter the SPDs response time is, the better is the overall protection function the SPD provides.
Coordination of SPDs:
The best effectiveness of SPDs can only be ensured through appropriate coordination of all SPDs with regard to the voltage protection level and the energy absorption. The necessary information to enable such coordination of SPDs can only be provided by the manufacturer, because the specific SPD design and construction may have a significant influence here. The larger an electrical system is, the more difficult and complex it is to achieve proper coordination because of the increasing distances, and therefore increasing conductor length and impedances, between the SPDs and the parts of the installation and the equipment to be protected, which may cause the various SPDs installed to operate independently from each other.
Total discharge current (Itotal 10/350 and Itotal 8/20):
This parameter is intended to specify and test for the maximum surge current stress in the terminal and related components of a multipole SPD, which are connected to PE. This is necessary to check for the accumulating effects and stress factors when several or even all modes of protection of an SPD are operated, because all other tests are performed on single modes of protection, only Itotal is particularly important for SPDs of type 1 as the stresses expected in a lightning equipotential bonding system are common mode, meaning impulse currents flowing simultaneously in all active conductors, as indicated in EN 62305-1 and -4.
Noise level attenuation:
This is realised by filters for limiting the electromagnetic interferences in the range of 150 kHz – 30 MHz, both in common and line to line mode, which show a specific characteristic to reach that protective behaviour. Such filters are added as an additional feature to advanced SPD designs for providing extensive protection against transients and all kinds of conducted interferences, with the aim of reaching electromagnetic compatibility (EMC) in a wide frequency range.
Pollution Degree:
The basic safety publication EN 60664-1 for insulation coordination for equipment within low voltage systems specifies and classifies four pollution degrees, whereby the micro-environmental conditions of the insulation must be taken into account for construction. Micro environment in this context means the immediate environment of the insulation, as compared to the macro environment, which describes the environment of the room or location where the equipment is installed. The micro environment often depends primarily on the macro environment and they are essentially identical.
Classification of pollution degrees (PDs):
PD 1: No pollution or only dry, non-conductive pollution.
PD 2: Only non-conductive pollution, except an occasionally temporary conductivity caused by condensation.
PD 3: Conductive pollution or dry non-conductive pollution which becomes conductive due to expected condensation.
This design parameter of an SPD should be thoroughly checked to determine its suitability for a specific application.
As a general guideline for domestic applications pollution degree 2 applies and for industrial applications pollution degree 3 applies. It may require particular attention in outdoor locations or under severe environmental conditions. e.g. for photovoltaic installations, public lighting and wind farms, industrial environments such as steel mills, cement factories.